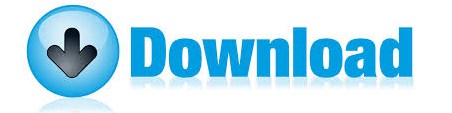
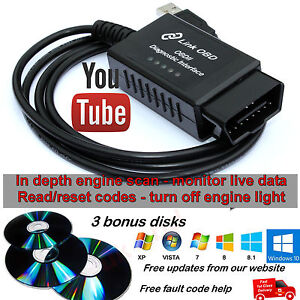
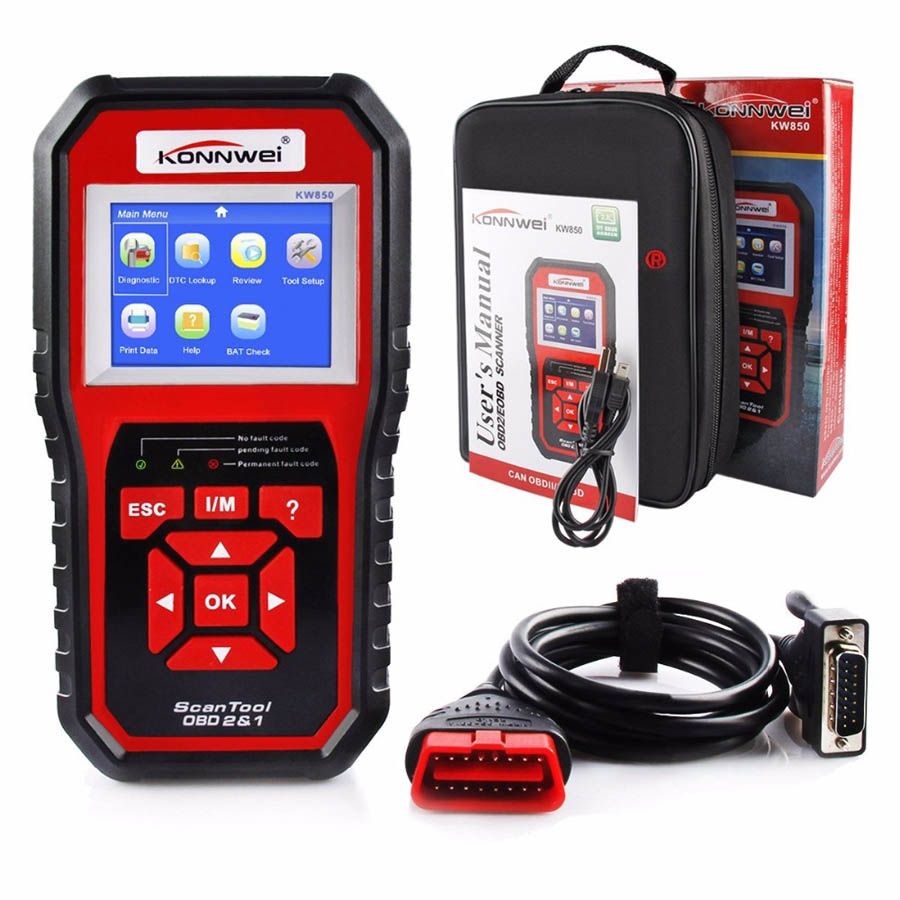
The MIL will turn off after three consecutive driving cycles in which the diagnostic runs without a fault.Ī history DTC will clear after 40 consecutive warm- up cycles without a fault.ĭTC(s) can be cleared using the scan tool. This information will be stored in the Freeze Frame and Failure Records buffers. The ECM will record operating conditions at the time the diagnostic fails. The Malfunction Indicator Lamp (MIL) will illuminate after two consecutive driving cycles in which the diag- nostic runs with the fault active. Throttle valve position checkback and monitoring is provided by two actual value potentiometers connected to the engine control electronics.Įlectrical system protection is not active. Each of them is able to position the throttle valve in emergency position alone. Motor and return spring are two separate energy sources. The motor positions the throttle valve against the return spring force. The throttle valve position, and thereby the actuator drive position checkback is provided by two potentiometers. When the actuator current fails, the throttle valve is re- turned to emergency operating position by a spring. Load adjustments indepen- dent of the drive pedal command can be implemented such functions are, for instance, idle control, speed con- trol, drive slip control, load shock damping, and similar functions. The TP sensors serve for engine load control according to the drive pedal command. The volt- age signal will vary from approximately 0.3 ~ 0.9 volts at closed throttle, to over 4.0 ~ 4.6 volts at Wide Open Throttle (WOT). The TP sensor sends a voltage signal back to the ECM relative to the throttle plate opening. The Engine Control Module (ECM) supplies a 5 volt ref erence signal and a ground to the Throttle Position (TP) sensor.
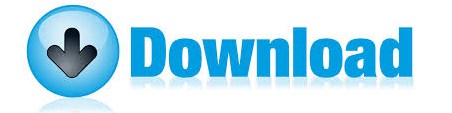